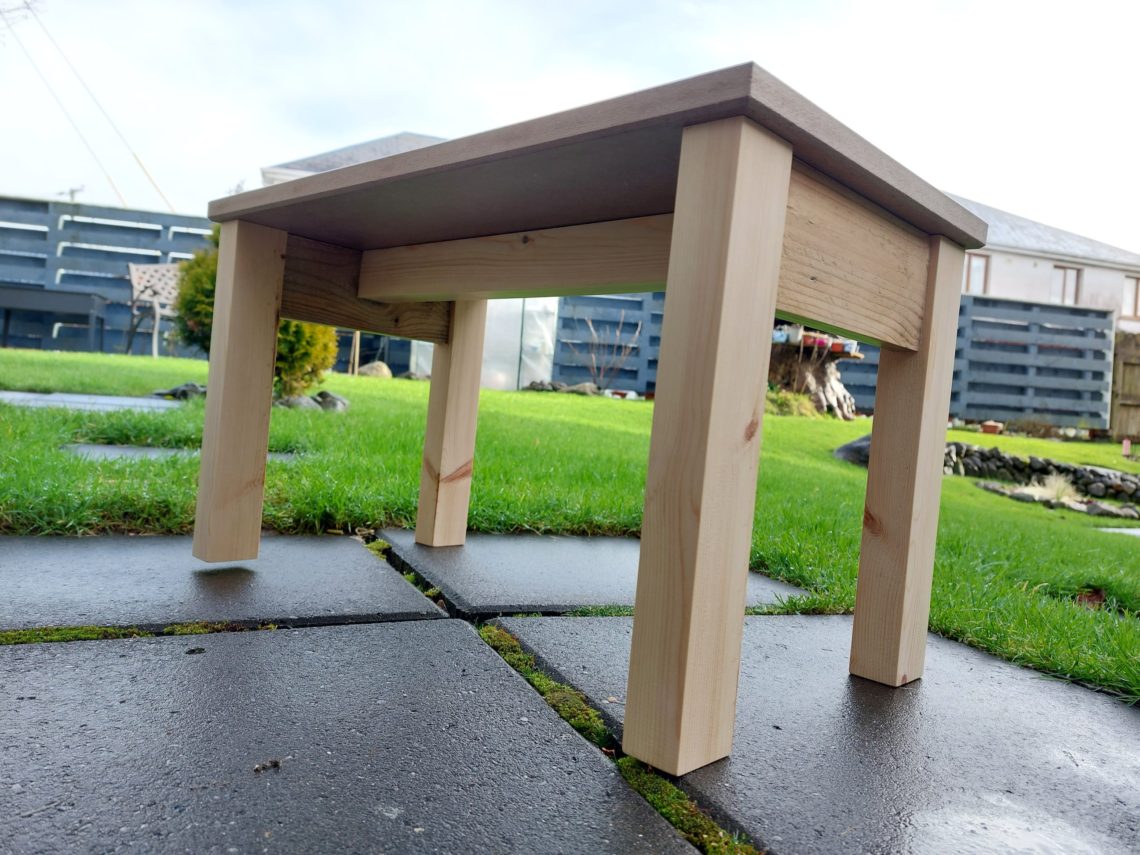
Utility stool
I built this stool especially for storing my linisher and a few buckets of paint underneath. Getting the most from the storage space I had was my goal as I was running out of ideas on where to keep all the paint. These buckets are usually the same height and all I needed was a clearance of 20 cm (~8 inches) from the floor to the stretcher. The stool had to be strong enough to handle the weight of a heavy tool and with these 2 requirements in my head, I started the build. I had everything I needed – timber, MDF, dowels, glue, tools and some finishes to choose from, plus 4 more years of experience compared to when I finished a similar project in the past to resolve the same, still recurring paint storage problem.
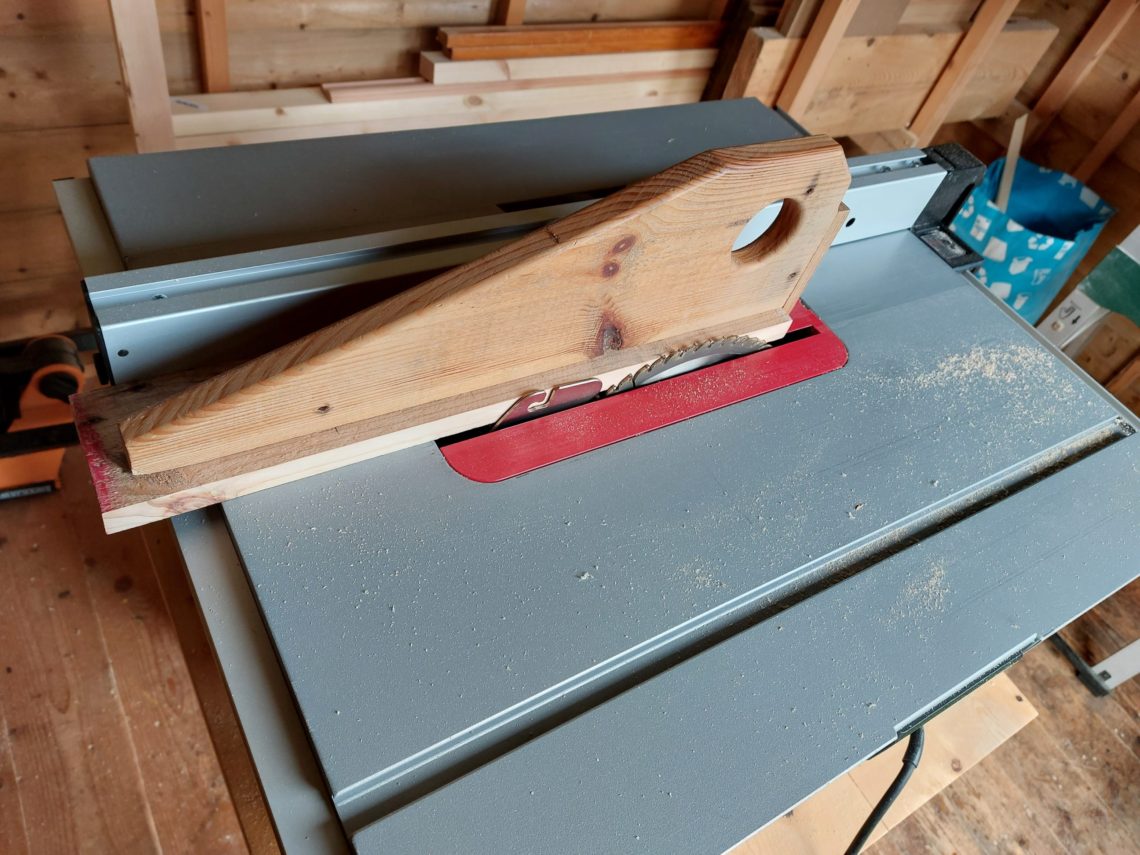
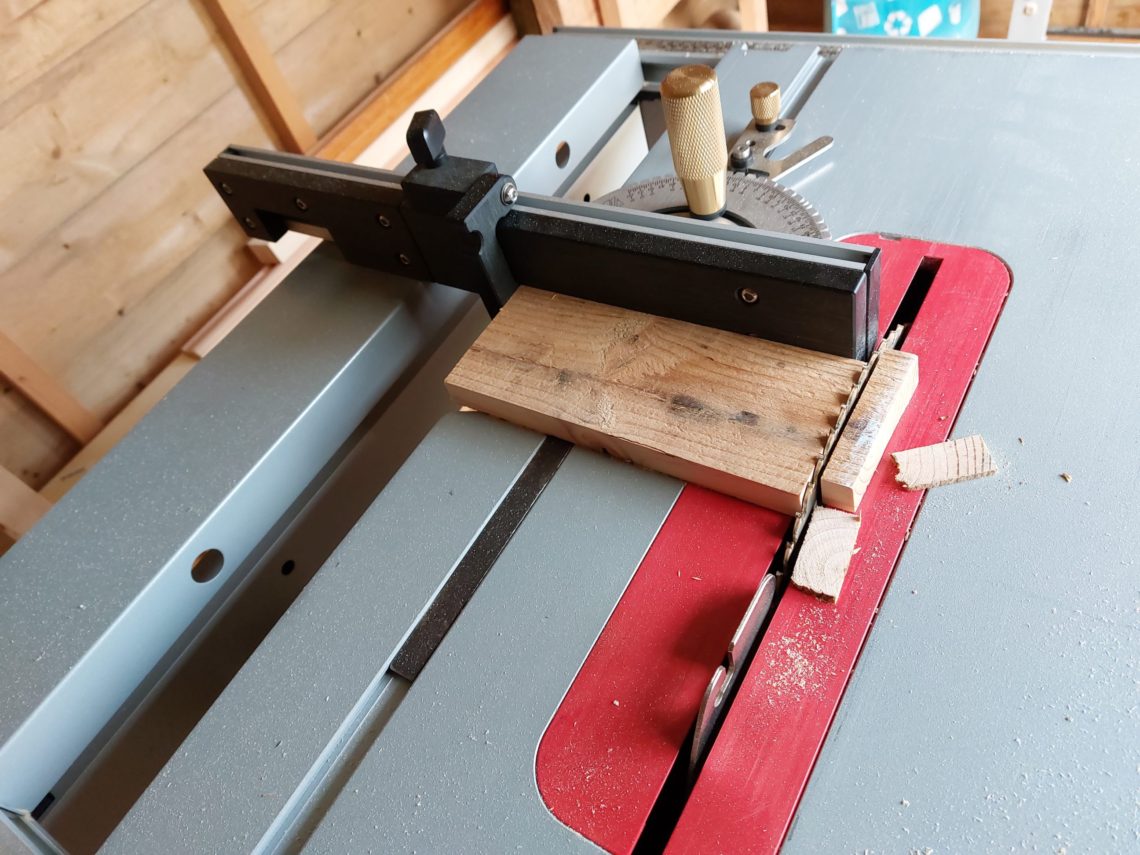
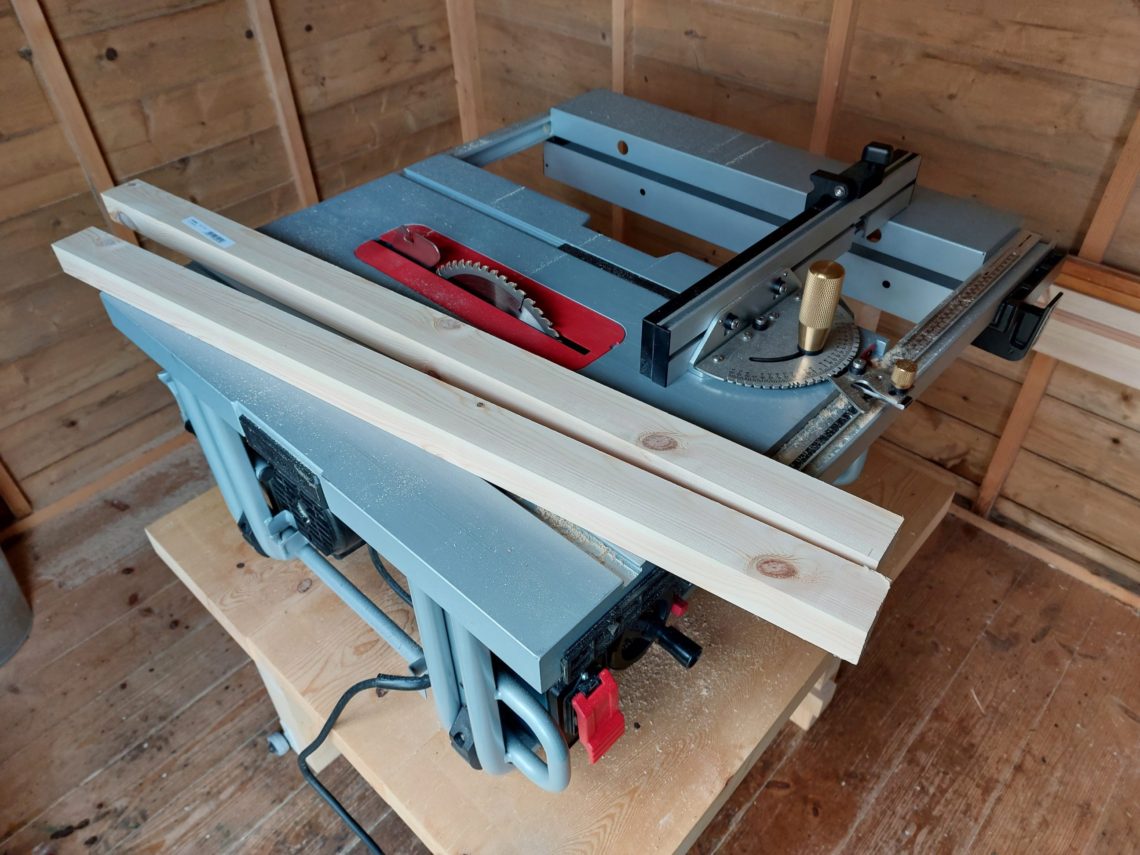
First I had to check with my metal detector if the pallet wood was metal-free and if it was safe to process on a table saw. Then I cleaned up the edges and cut 2 identical pieces for the apron. Next, I cut 4 legs and the stretcher, they were ~30 and 50 cm long respectively (~12 and 20 inches). Cutting MDF sheets to size on a small table saw is always challenging, sometimes you need to use its components in a weird way, and by components, I mean a fence or a mitre gauge, they can be flipped over to make a cut. That was what I did to cut off a thin strip from that sheet – I moved the fence to the left, pulled out the extension arm on the right, to support the workpiece and carefully made the cut. The off-cut piece was supported and guided by the push block, tight against the fence. Probably a 3D push block would be better, the yellow “gripper”, but a homemade one worked as well. I could only guide the bigger piece with my right hand to some point and not too strong – otherwise, I could pinch the blade and create a dangerous situation. But, if you know what you’re doing and what the risk is, you can use a table saw like that – I guess.
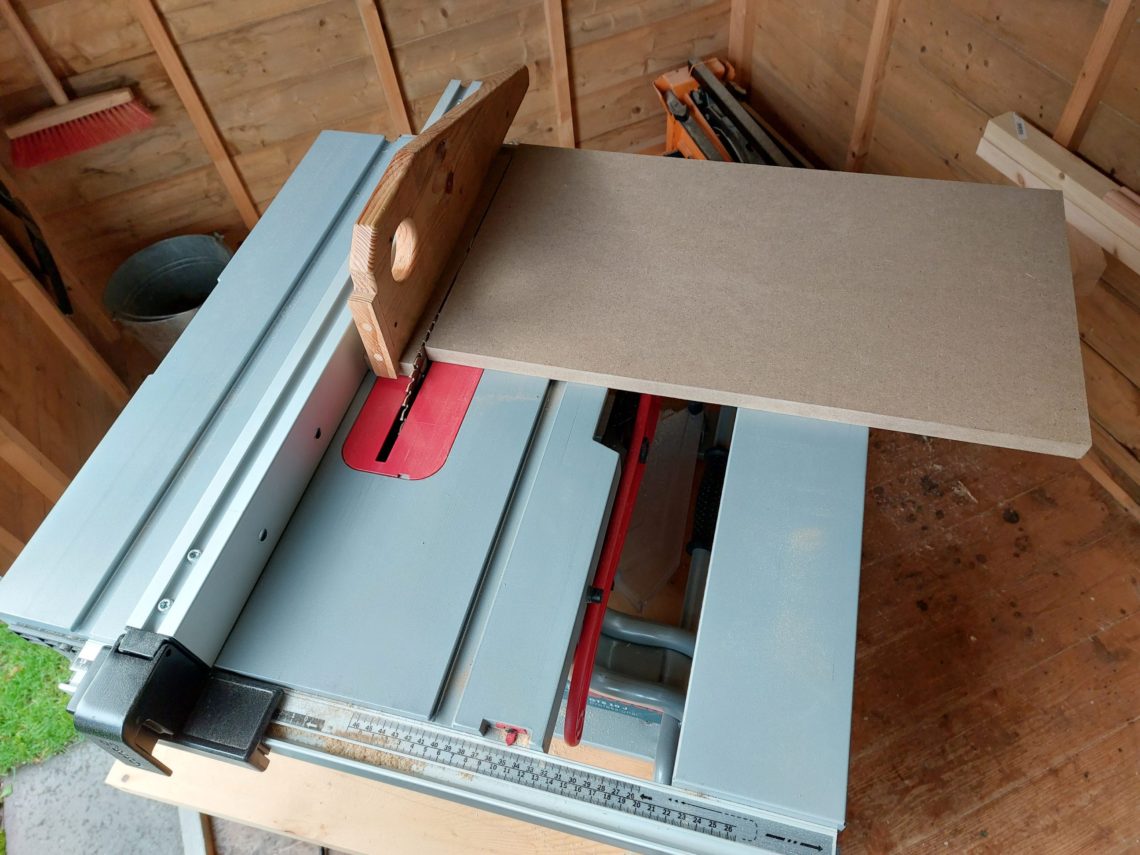
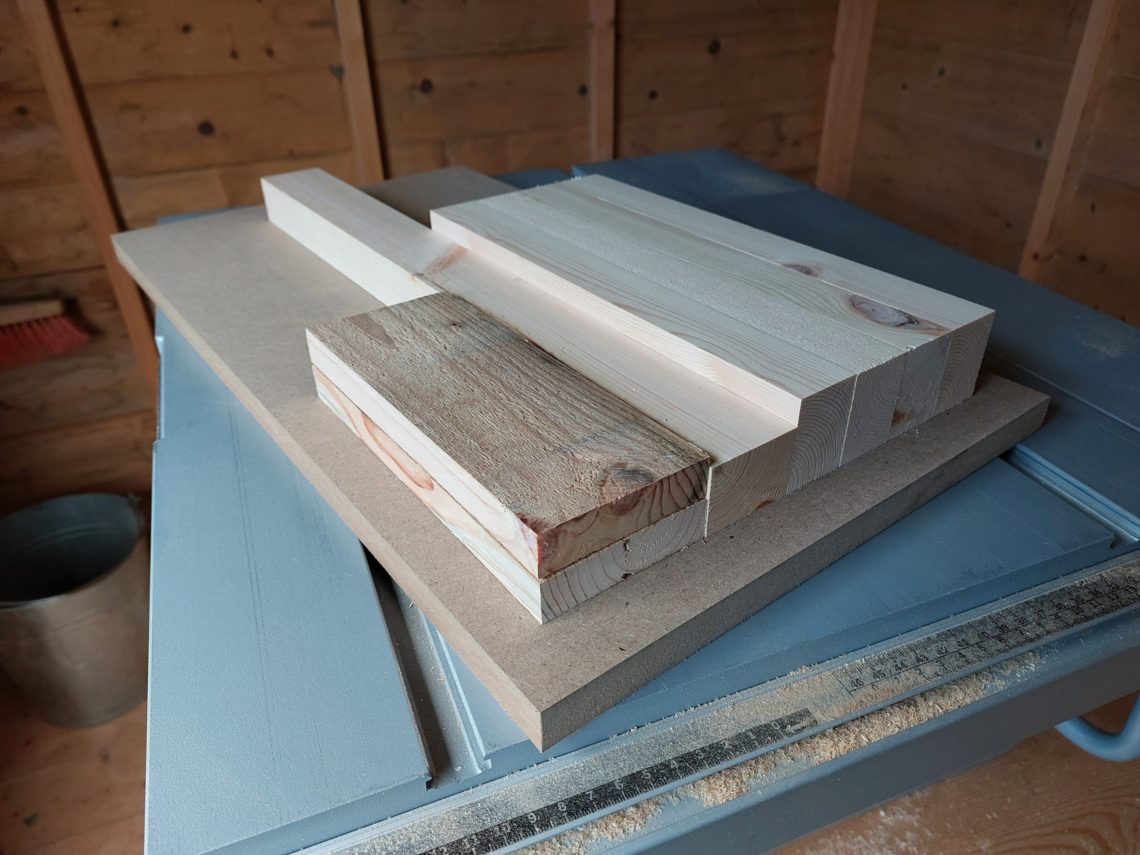
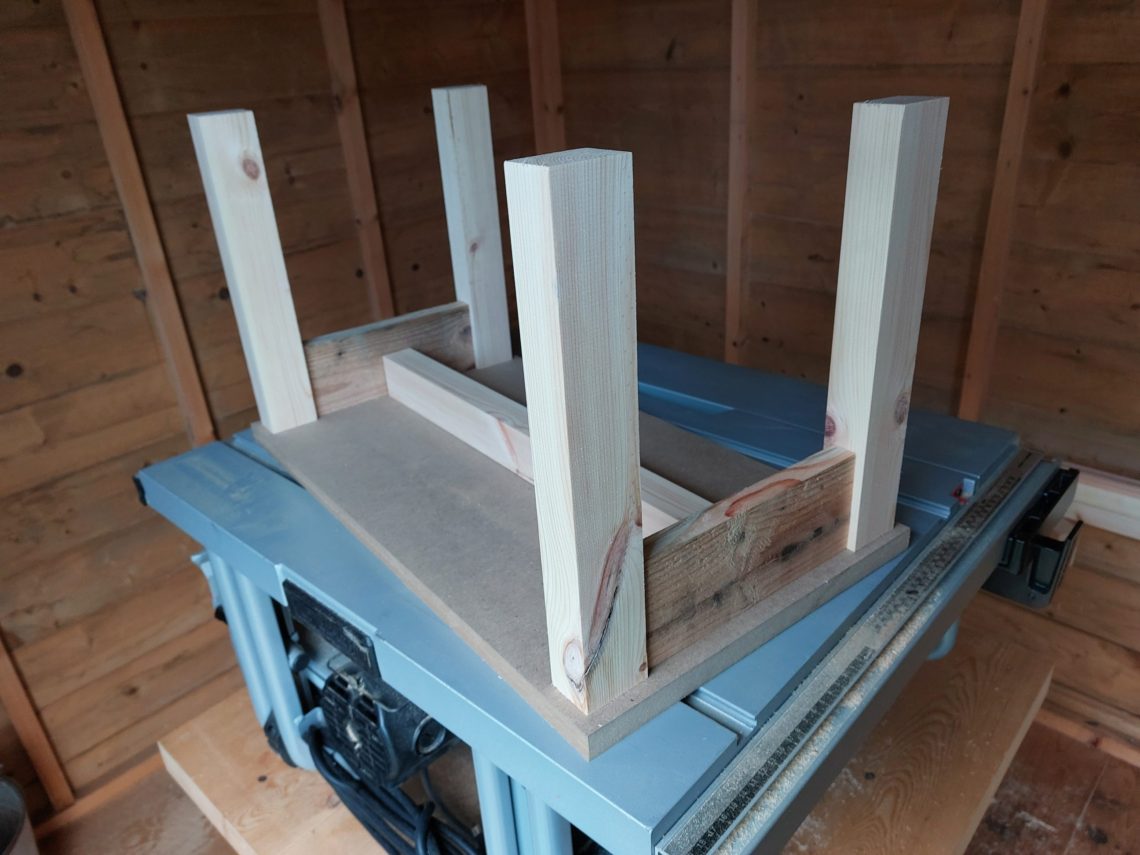
All the material I needed was cut to size with a single tool, which saved me some time that I could use in the next step, which was dowelling. I marked all the lines I needed for aligning my jig and drilling holes. The dowels were equally nested into both joined parts, except for the stretcher and the aprons – due to their thicknesses. Some of them were also predrilled with a 3 mm bit first and then finished with the 10 mm one. It was supposed to minimise drill bit wander but it didn’t work as planned and some correcting clamps had to be used later on, during the glue-up. Anyways, it all ended very well, the stool was square and flat in all planes.
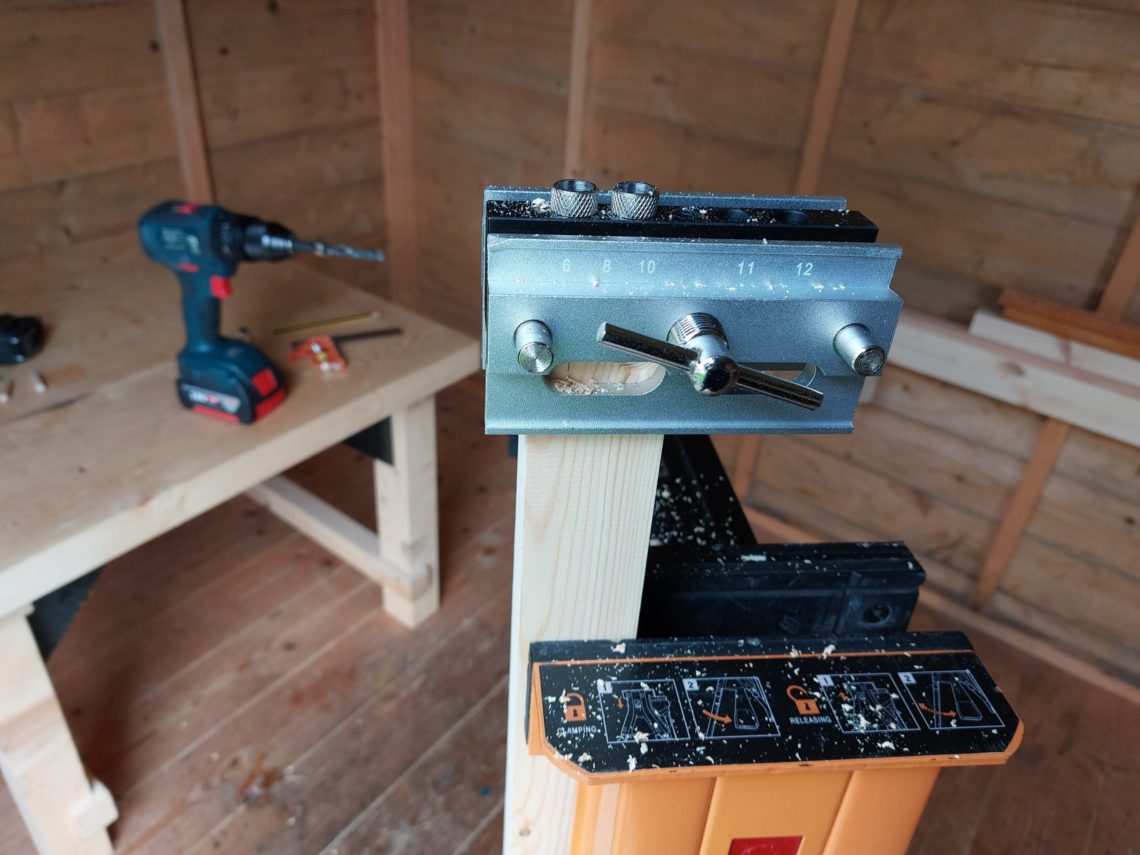
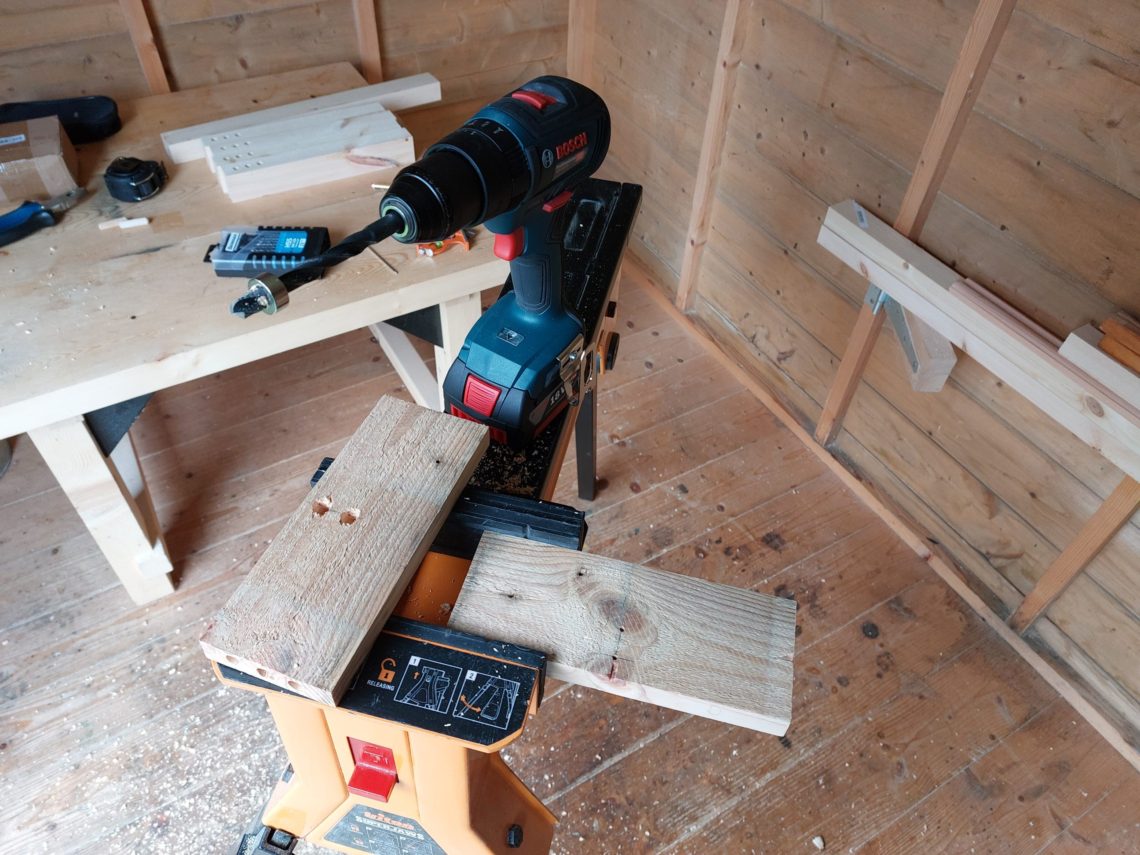
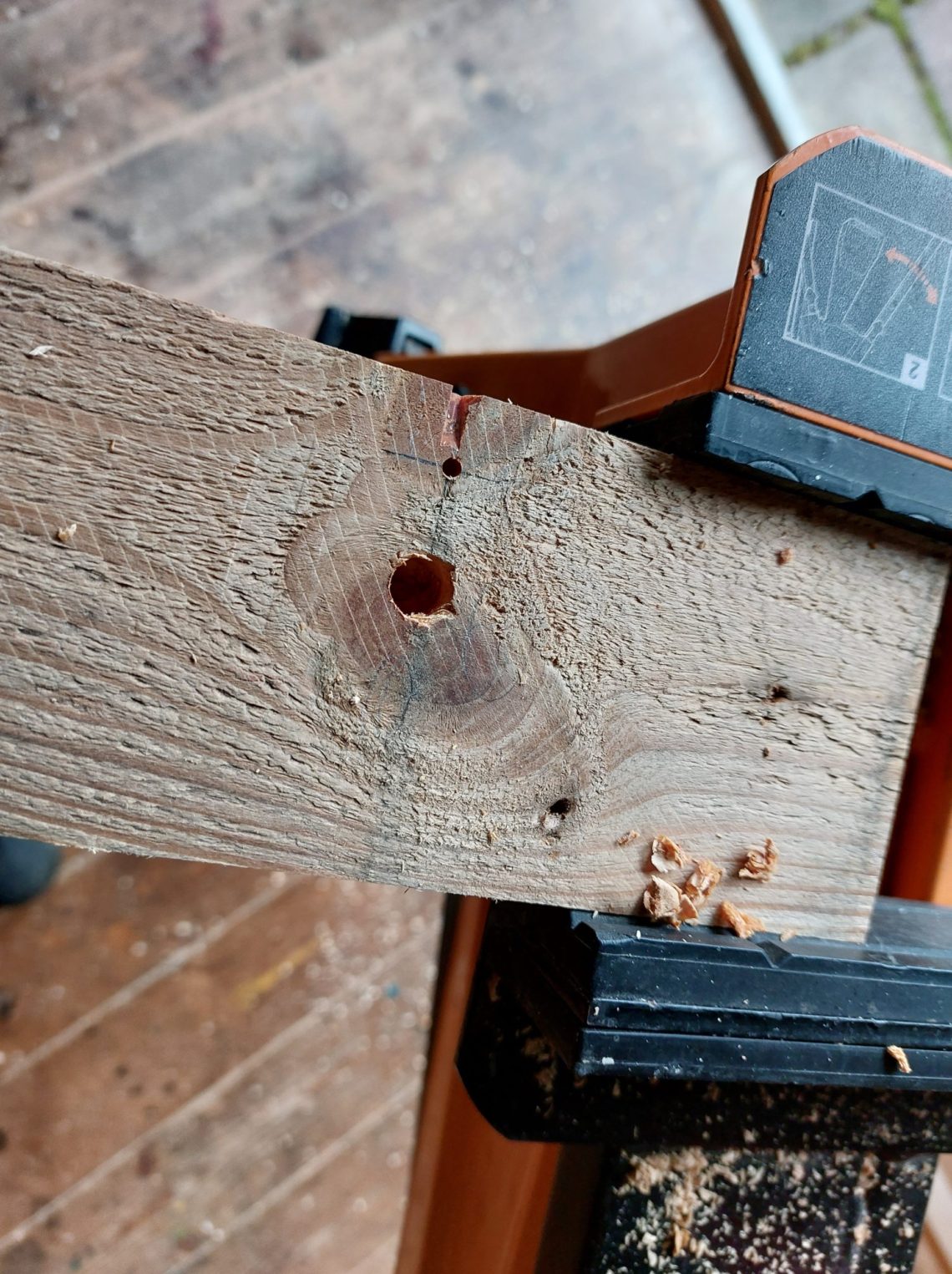
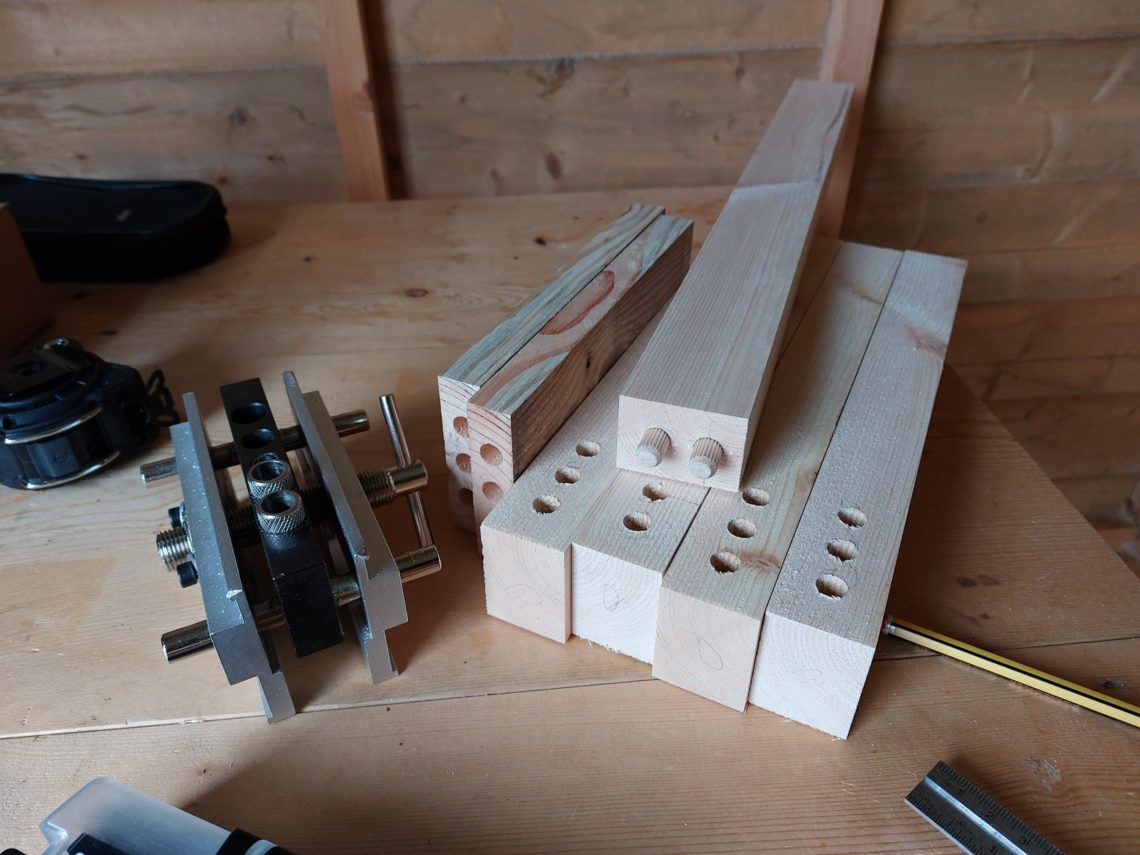
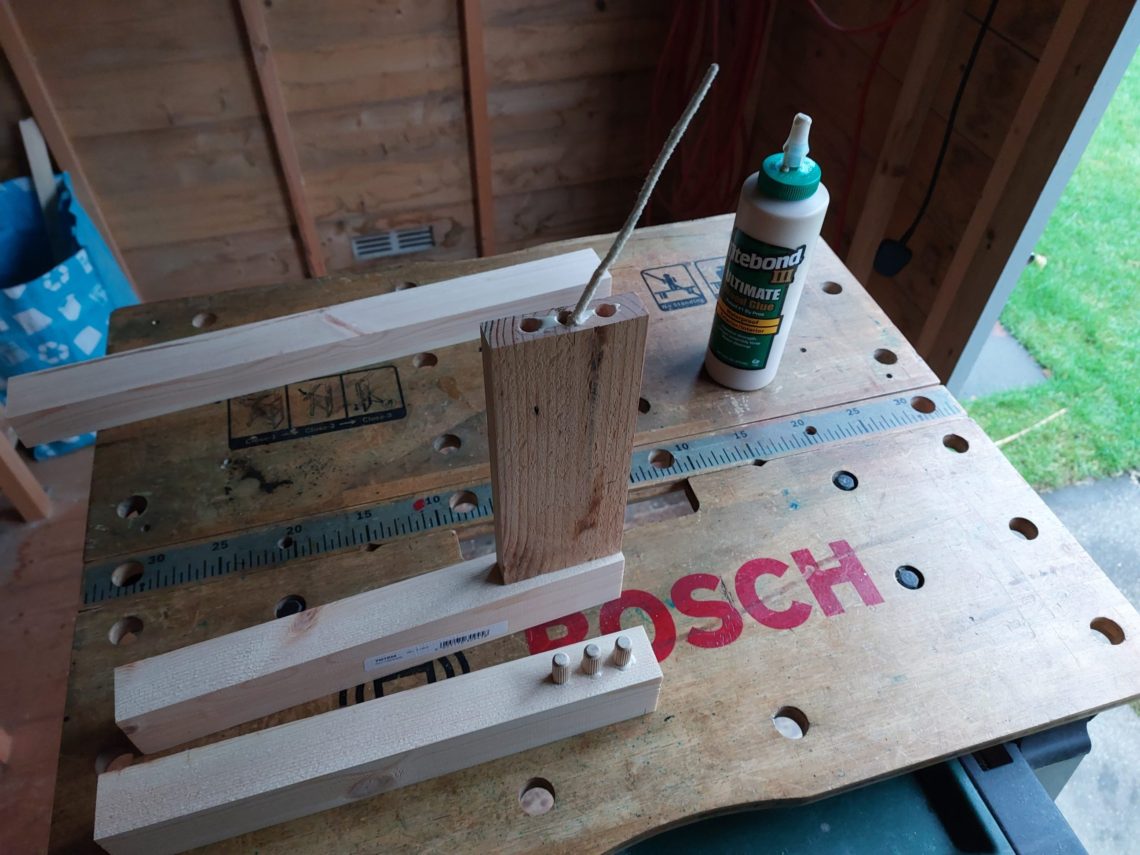
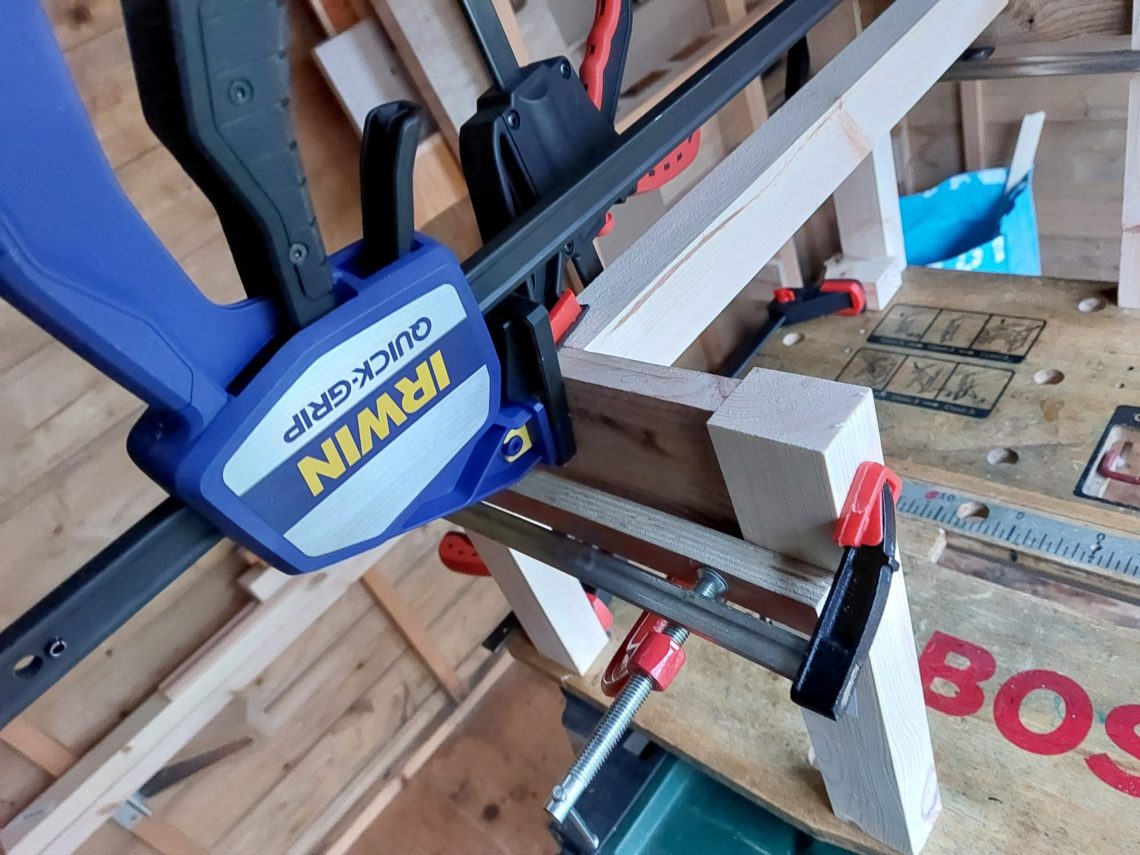
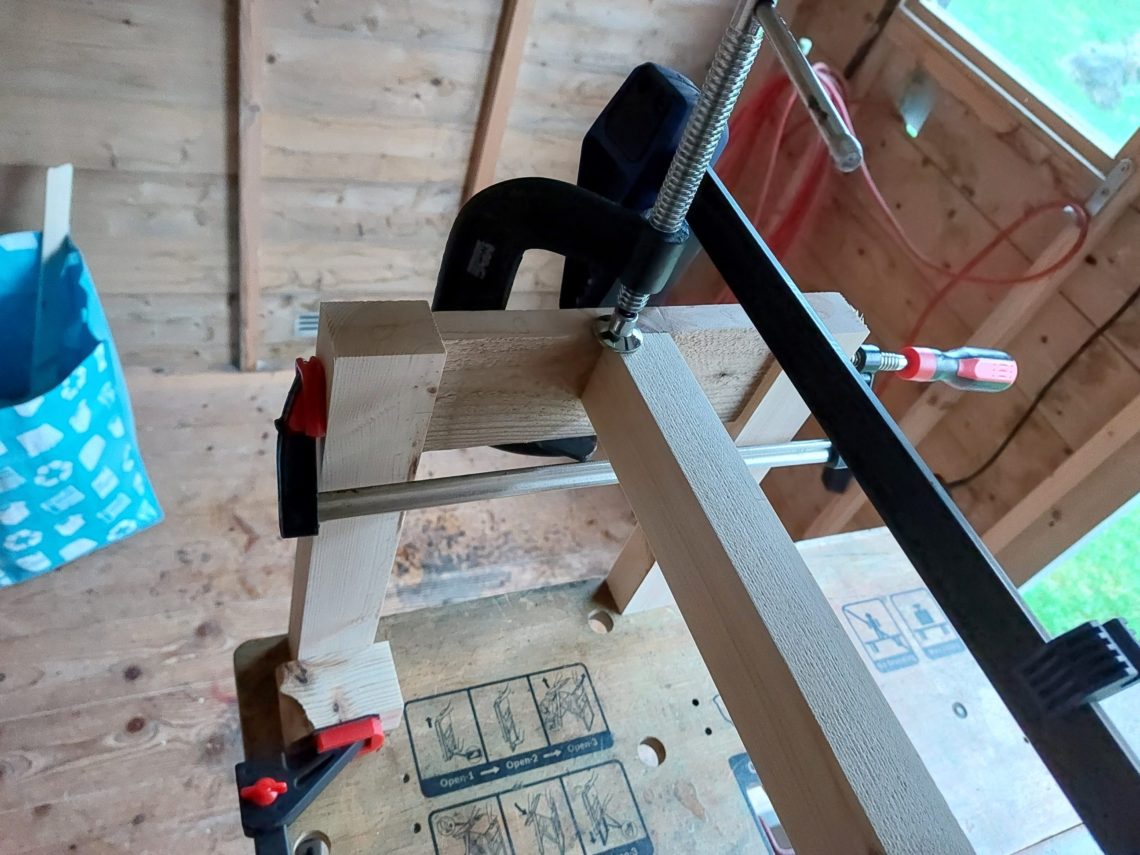
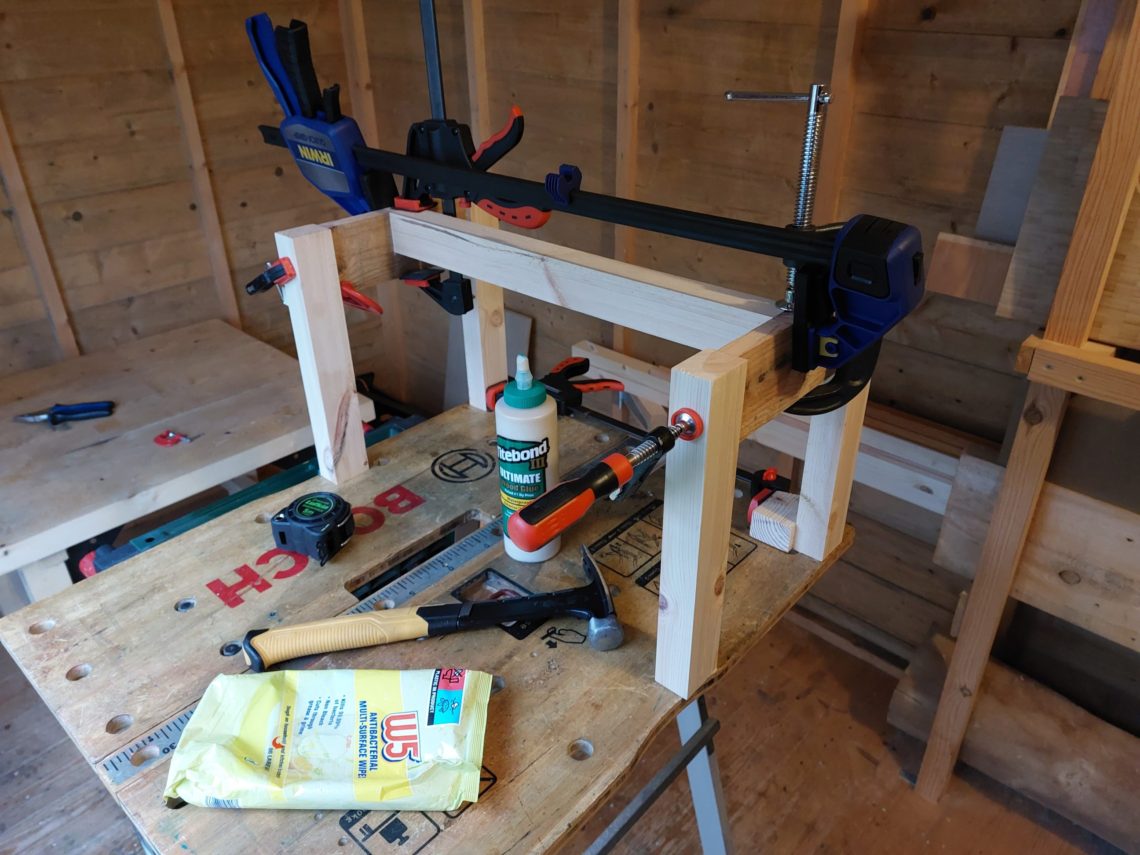
With a router, I chamfered the “tabletop” edges, sanded the base and drilled several holes for dowels that were going to permanently connect the base with the top. Even though this stool was meant to be shop furniture, I made an effort to build it metal-free, without visible fasteners – unlike the other platform I made in the past. I used bigger, 10 mm dowels for the corners and smaller, 8 mm ones, for the stretcher. I only did it that way because I didn’t have enough 10 mm dowel centre point pins and I had to use smaller ones. One more thing worth pointing out – vertical dowels didn’t interfere with already glued, horizontal ones. When the drilling points were transferred to the MDF and left small indentations, I enlarged them with brad point bits and finished with HSS ones – the only bits suitable for both MDF and dowel joinery due to their properties and the shape of their tips. Brad-point bits clogged up and couldn’t be used as close to the edges (faces) as regular bits, with pyramid-shaped tips. I applied generous amounts of thick Gorilla wood glue to the holes, having in mind that MDF could potentially soak up more than solid wood. All the glue squeeze-out was removed and wiped off after 20 minutes and when the clamps were removed, the stool was ready for the finish.
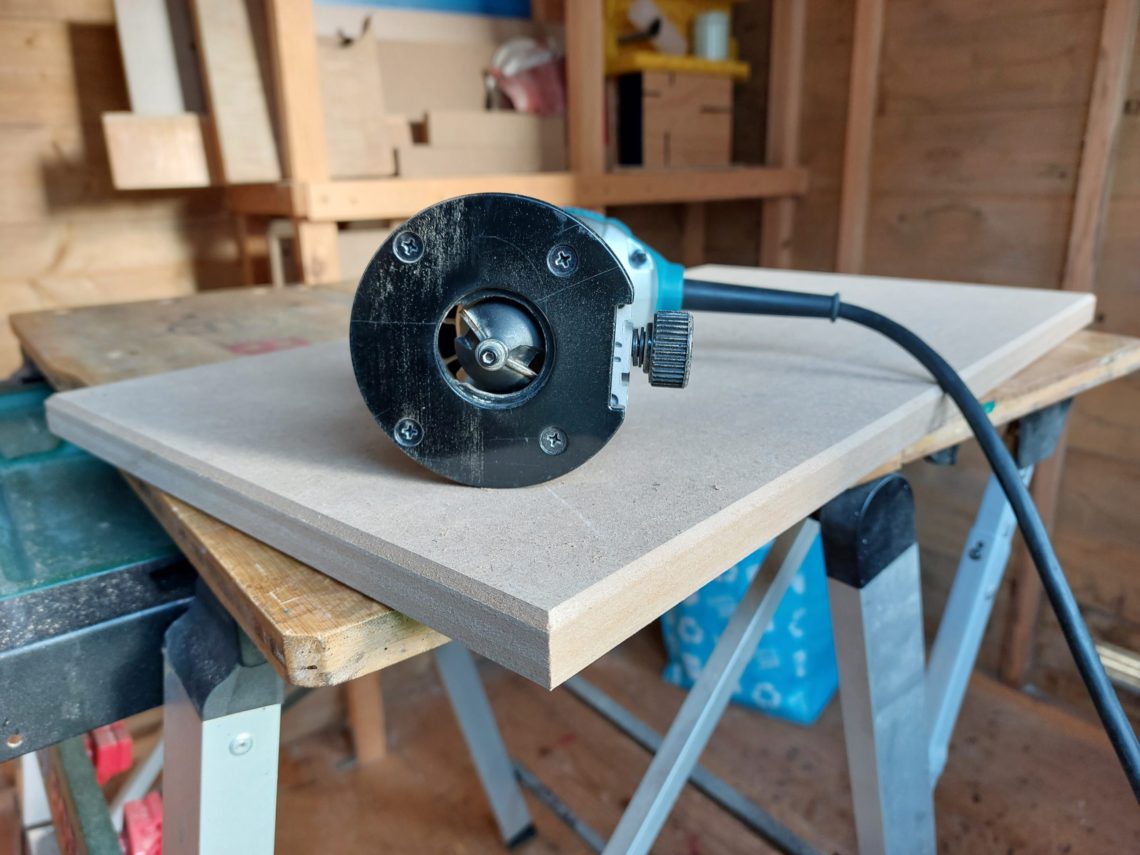
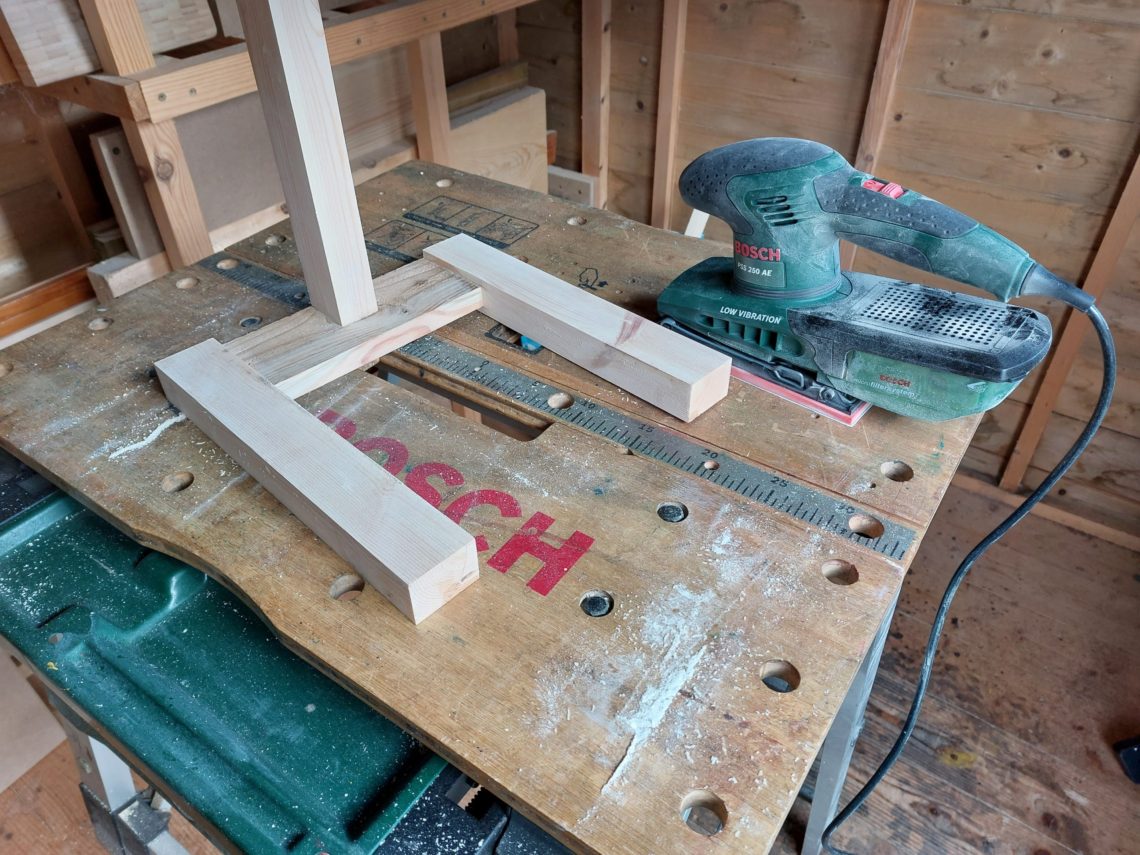
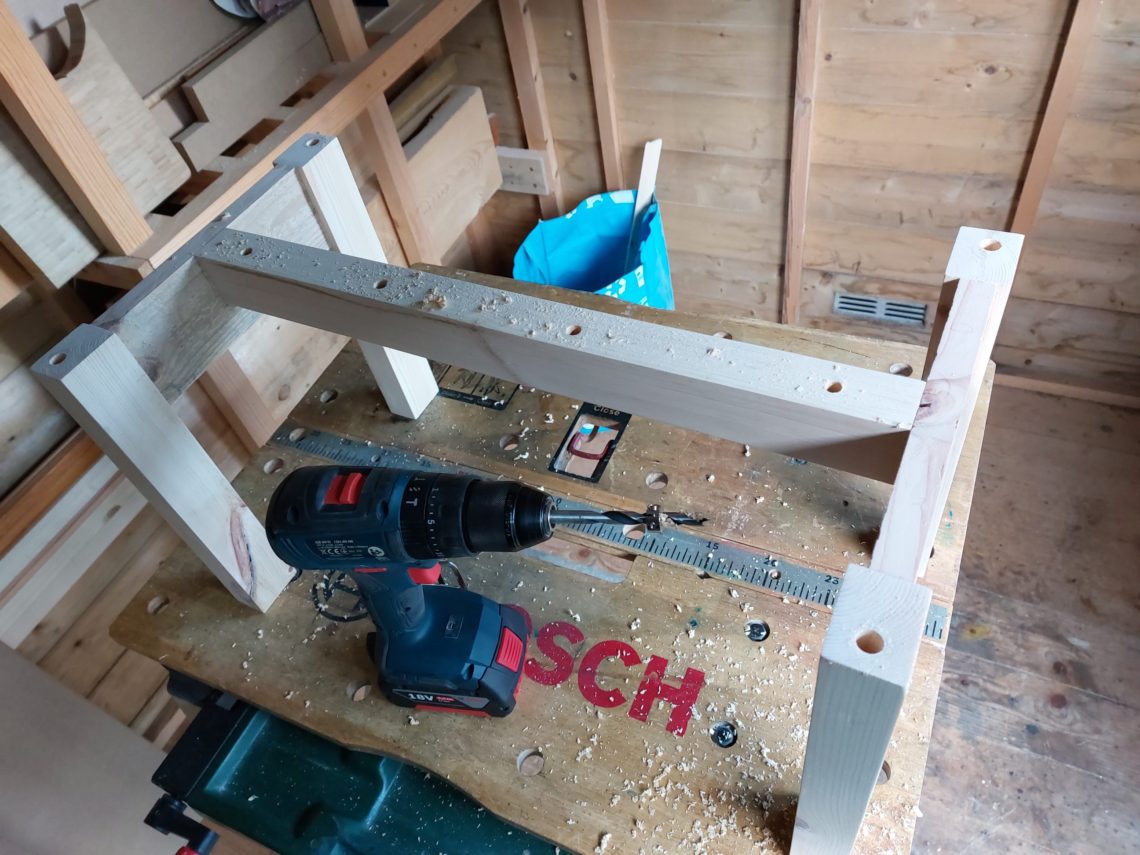
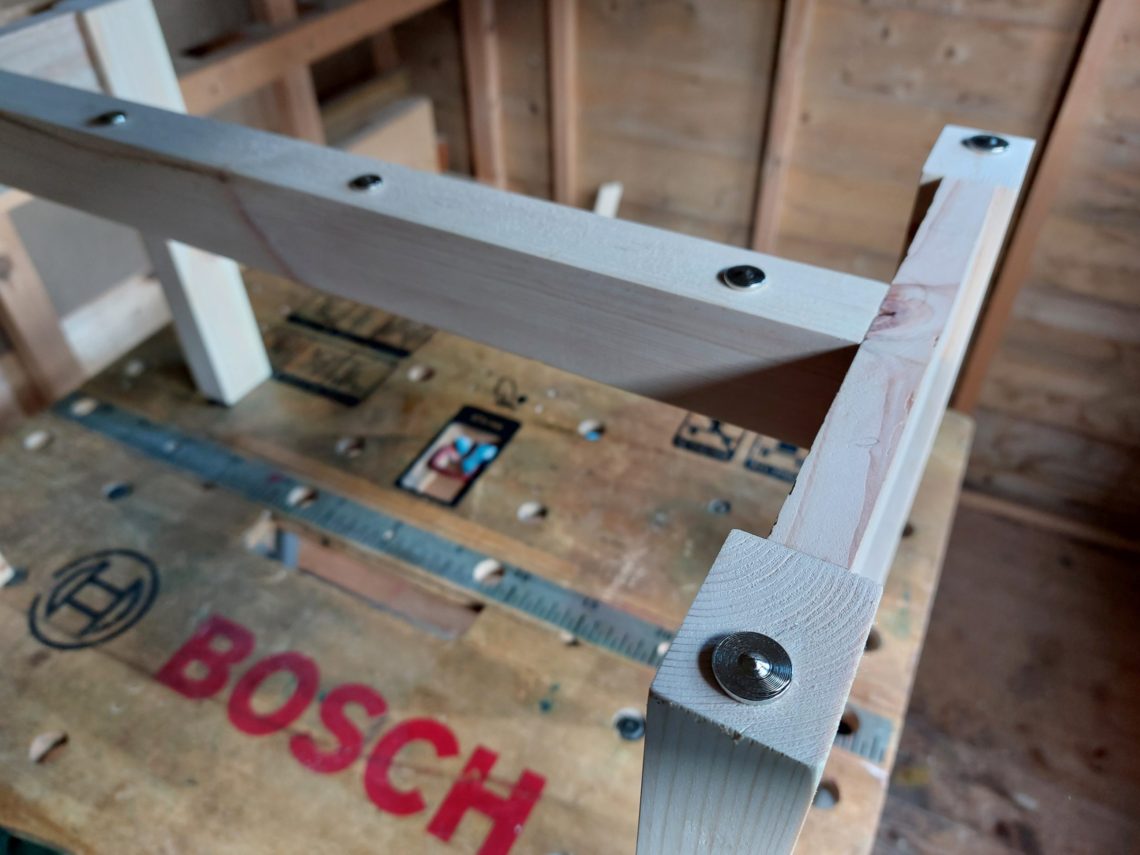
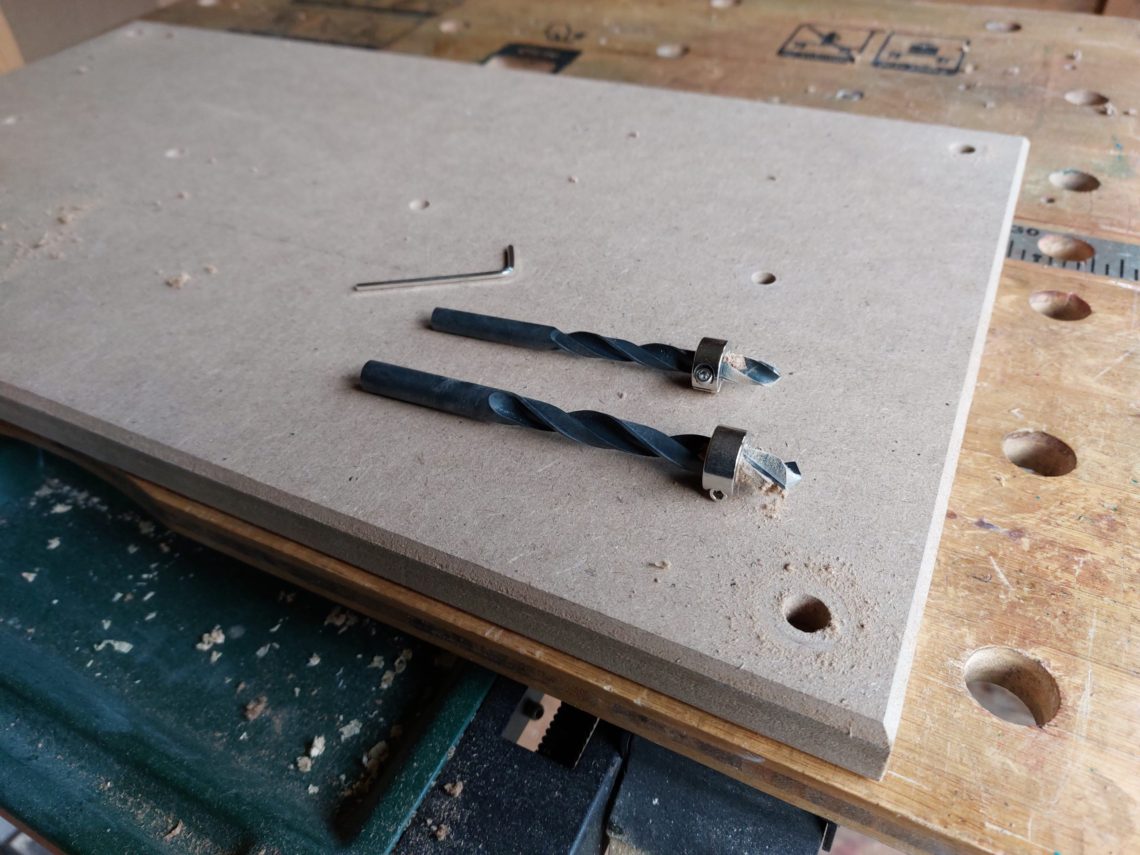
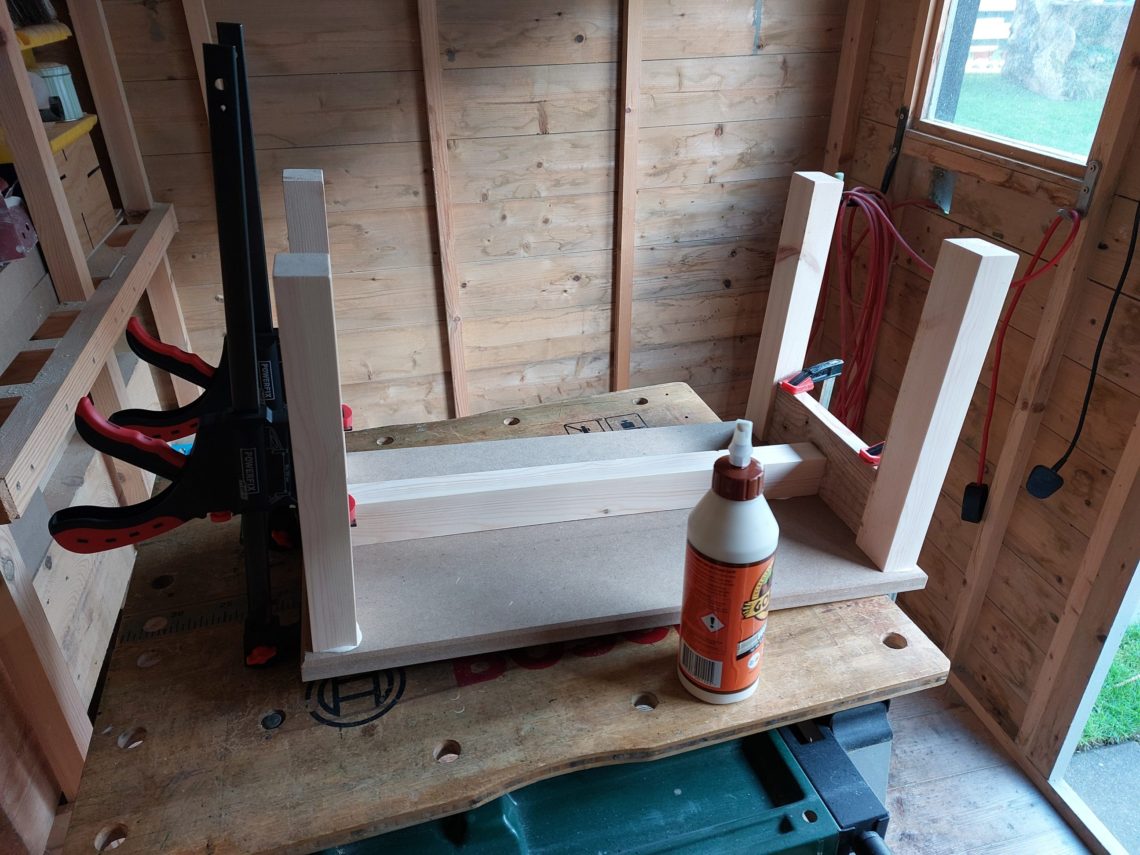
I chose to finish it with wax, for 3 reasons; 1 – weather, the temperature outside wasn’t perfect for any other finish, it was only warm for a few hours a day and not overnight, 2 – I’ve always wanted to try wax on MDF and 3 – it was the cheapest and thus the most appropriate finish for shop furniture. I applied wax with a soft cloth, buffed it with a buffing wheel attached to a drill and what was left in the corners was removed with nylon brushes. One coat, simple, cheap and quick. The colour of MDF only darkened for a short period of time, right after the wax was applied and then turned back pale. It looked the same before and after, but its water-repellant properties improved and that was the plan. The type of wax I used was beeswax and not finishing wax, probably that fact determined the final look. The stool was ready to use straight away, I placed it just in front of my old platform, and it did exactly the same job as the platform – stored tools on top and buckets of paint underneath. Custom-sized, heavy-duty and with a clean, classic look. Even though it looks like a table, it’s way smaller, just like a stool, but there is one more feature that makes it different from a table – a single stretcher in the middle and not 2, parallel pieces of an apron on the opposite sides.
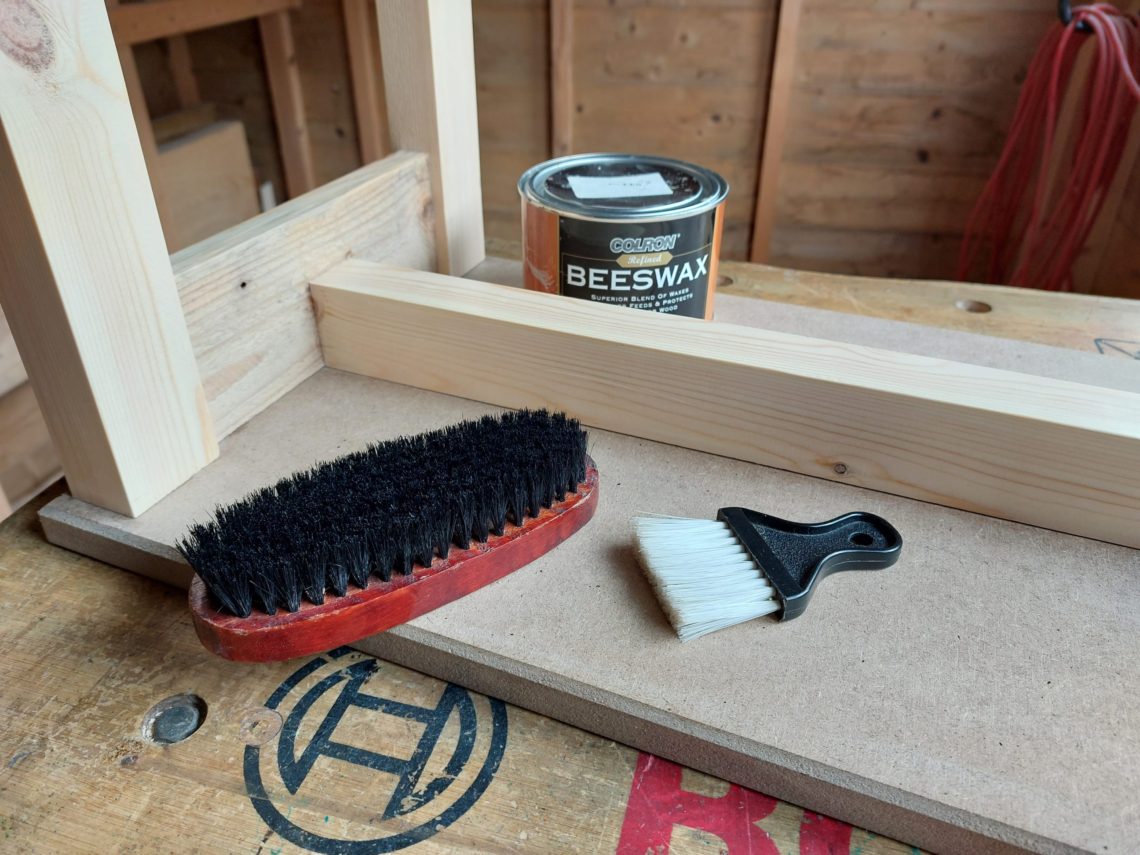
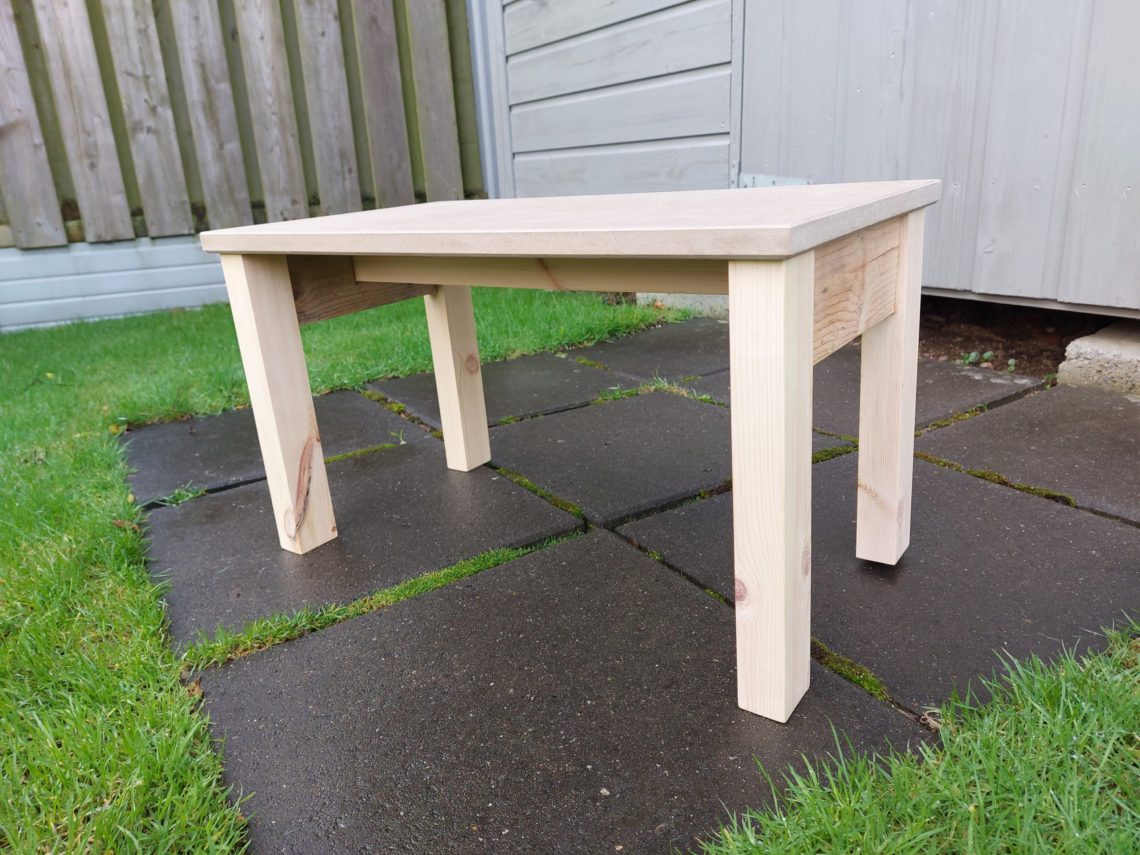
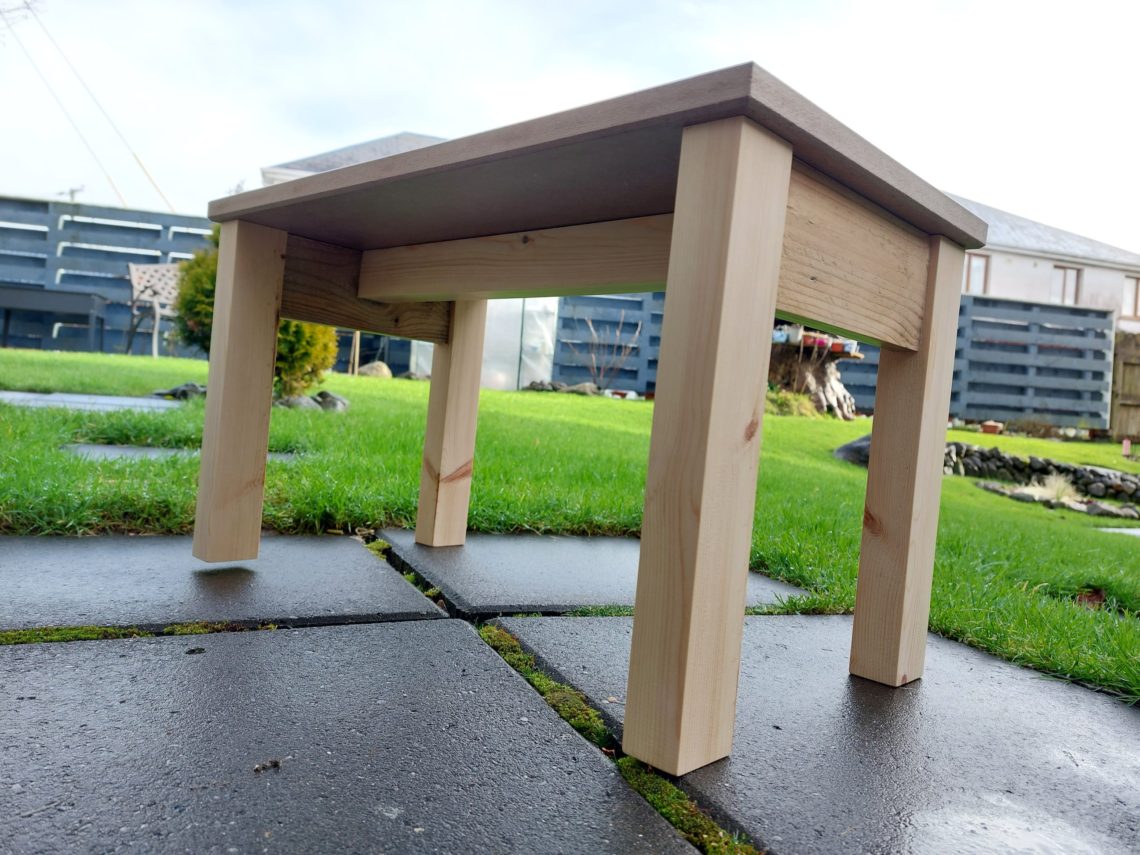
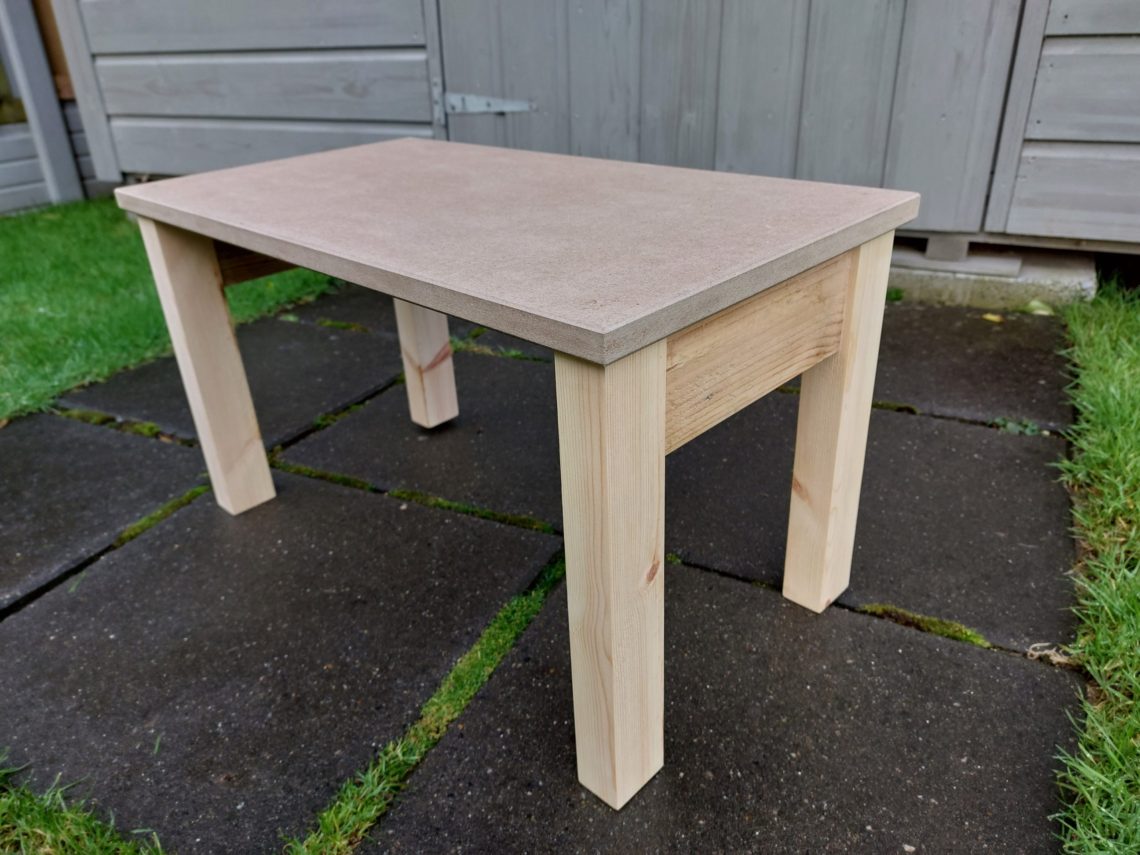
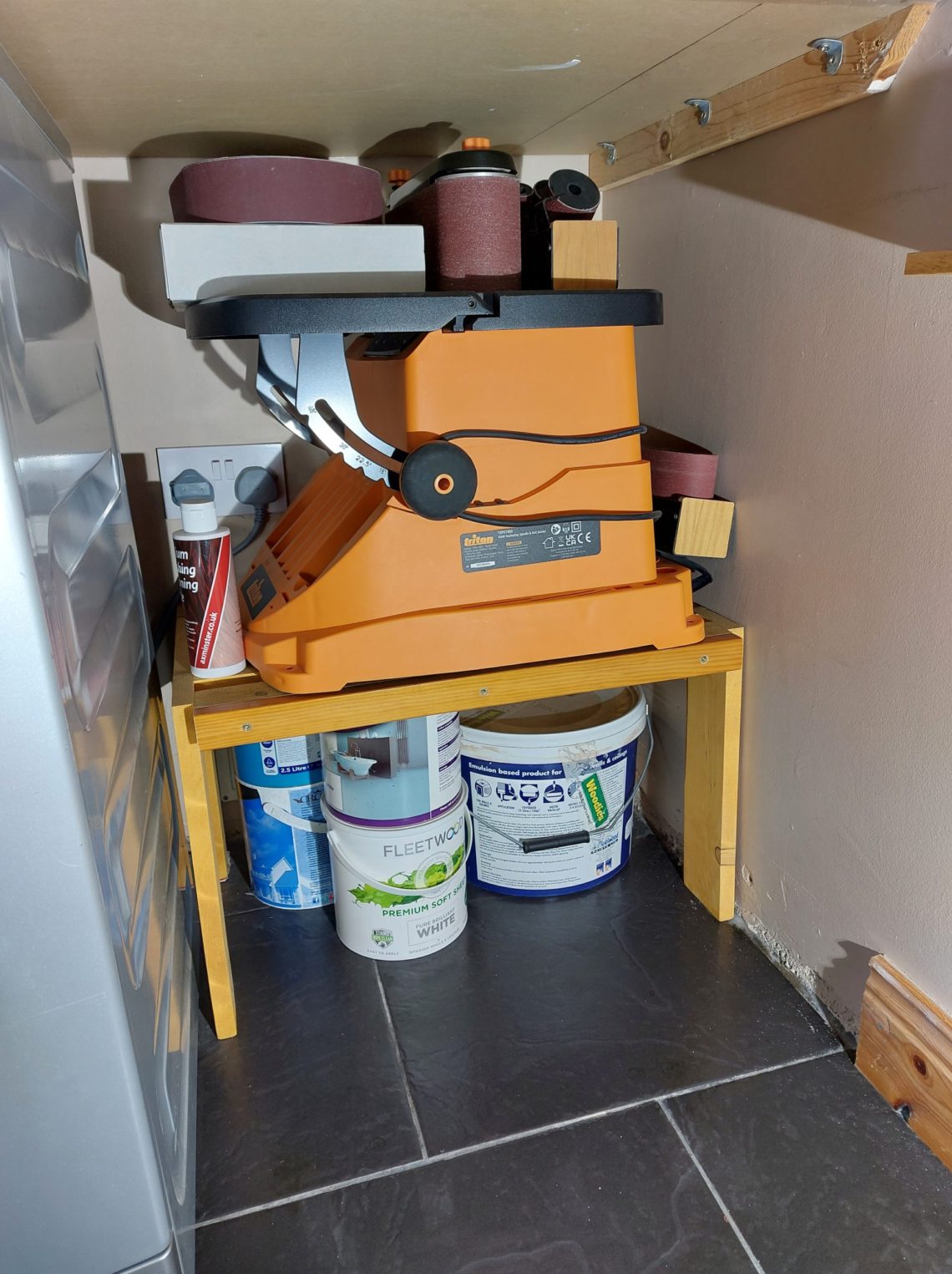
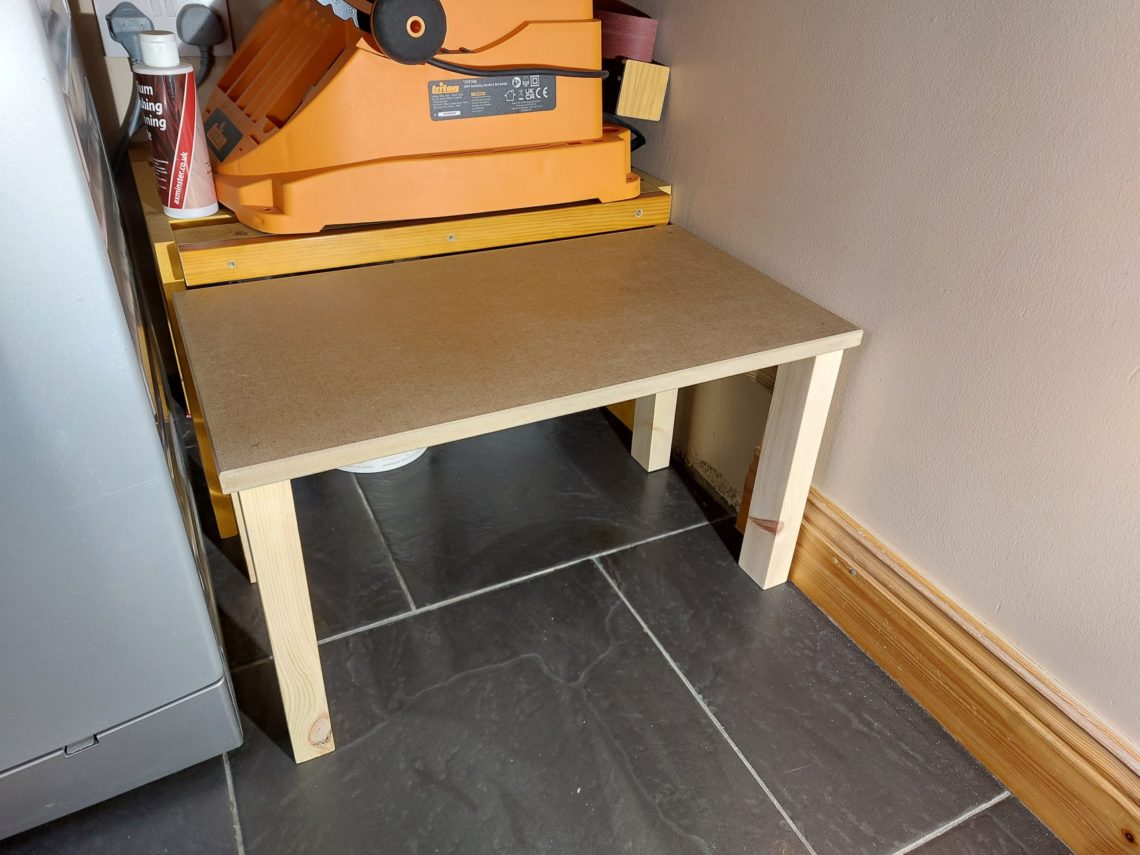
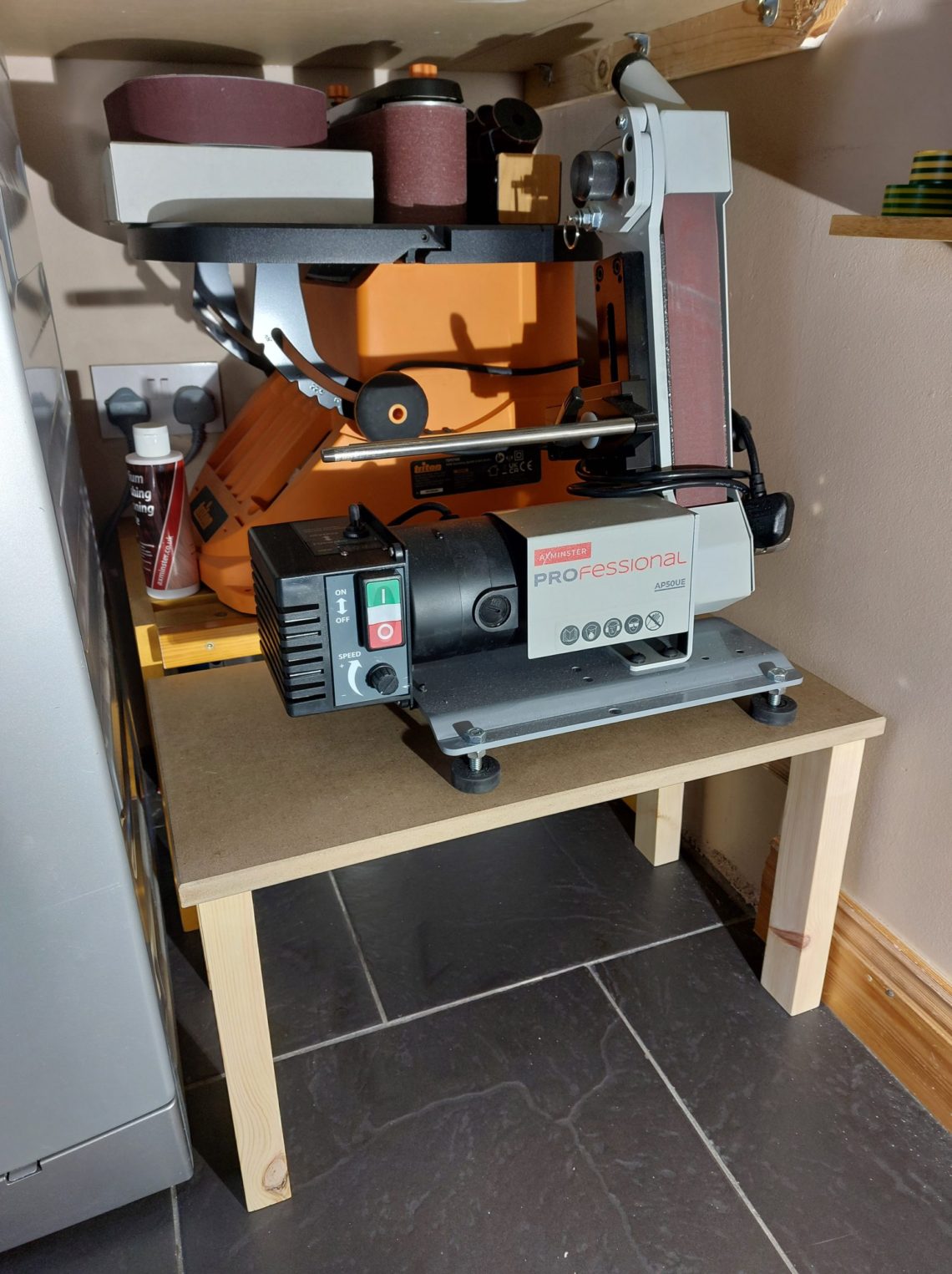

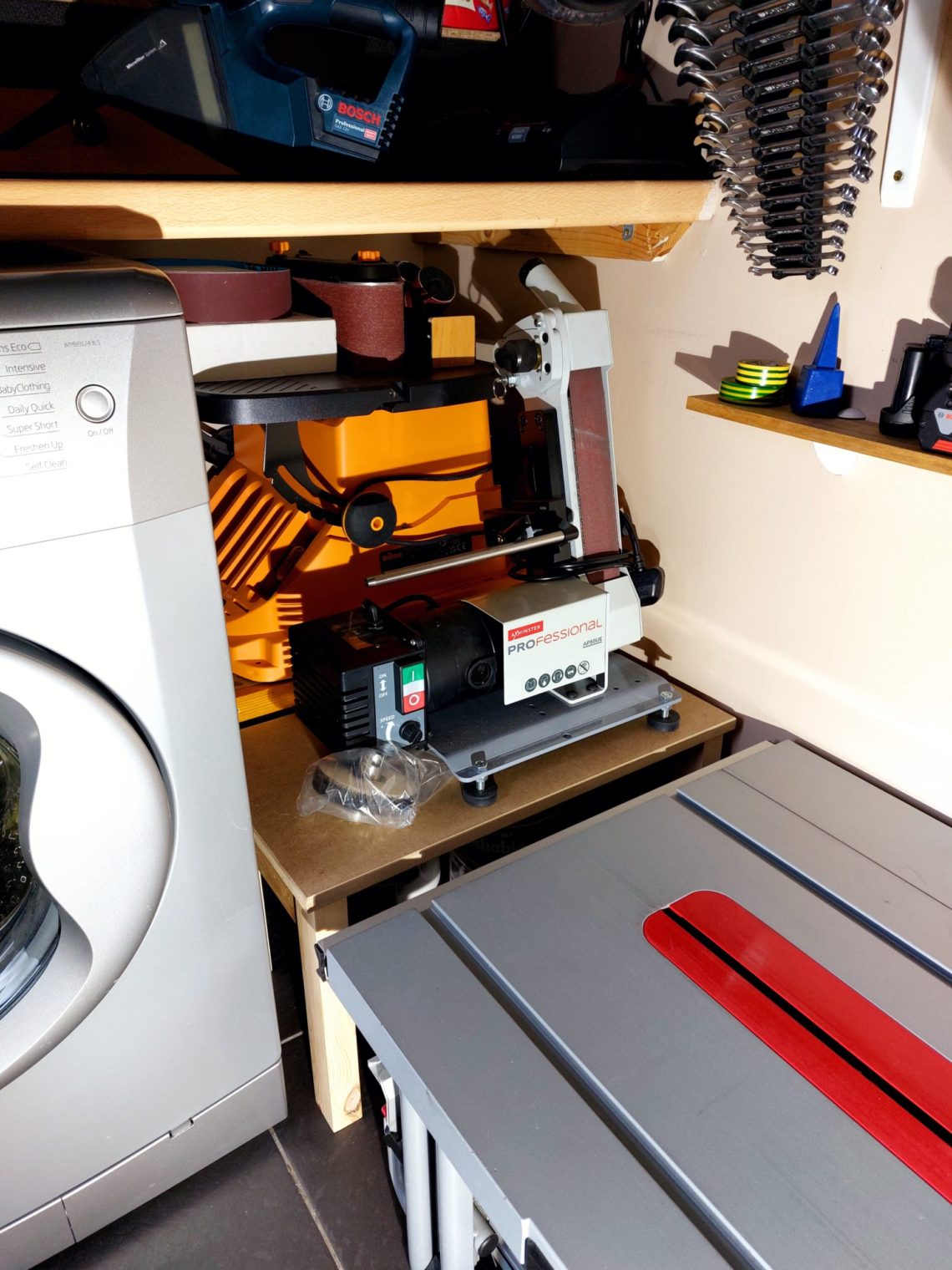

